新たな技術への挑戦
ケイ素とも呼ばれるシリコンは、地球上で酸素の次に多い元素。当社はありふれた物質を使って時代の最先端を追い続け、電子部品加工の革新を実現させてきました。シリコンウェーハに行う熱処理を、コンピュータでシミュレーションするシステムの開発プロセスにも、SUMCOの真骨頂が凝縮されています。
MISSION
シリコンウェーハに行う熱処理を
コンピュータ上でシミュレーションする技術を開発せよ
お客様である半導体メーカーが、シリコンウェーハに行う熱処理をコンピュータ上でシミュレーションできないだろうか。熱処理の条件が多様化し、ウェーハ品質とのインターラクションが目につき始めた2006年、SUMCOの九州事業所で新たなプロジェクトチームが発足しました。
加工技術はお客様にとって大切な資産。どれだけの温度で、どれだけの時間と速度でシリコンウェーハに熱を加えるかは企業秘密であり、SUMCO側にも教えてもらえません。雲をつかむような挑戦が実を結ぶまでには、10年もの歳月を要しました。新機軸のシミュレーションシステムの開発工程を支えたのは、「技術で世界一の会社」というSUMCOの誇りでした。
MEMBER
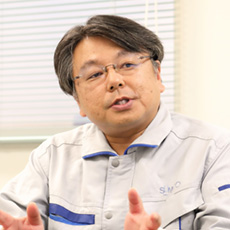

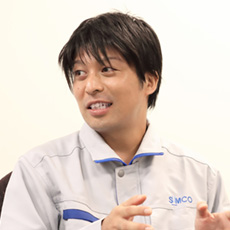
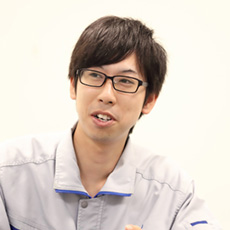
※所属部署は取材当時のものです。
熱処理の多様化に伴い
ウェーハの強度向上が課題に。
スマートフォンやパソコン、デジタルカメラをはじめとする、電子機器を支える半導体を完成させる過程で、シリコンウェーハ上に電子回路を作製するために、熱処理が複数回施されます。2006年ごろから、各デバイスの進化に伴って多くの半導体メーカーが新型の熱処理装置を導入し始め、最高到達温度や熱を加える時間、加熱速度が多様化しました。その結果、ウェーハが割れたり、変形したりするという問題が発生するようになりました。
「我々もウェーハの強度をさらに上げる必要性を感じ、お客様の熱処理を模擬できるコンピュータシミュレーション技術の開発に着手しました」
こう話すのはプロジェクトを統括したT.O。まだ世界のどこにもないシミュレーションプログラムをつくる役割を託されたB.Kは、「面白そうな話だな」と感じる一方、「本当にできるのだろうか」という不安も抱いたと言います。
何よりの難題は、お客様がどんな熱処理を施すかわからないこと。技術流出を防ぐため、どのような電子回路をつくり、どのような条件で熱を加えるかを企業秘密とするのは当然の話です。打ち合わせを重ねるなかで、何らかの糸口を見い出せるかもしれませんが、保証はありません。シミュレーションに不可欠な情報が得られない難しい状況で、SUMCOの挑戦が始まったのです。
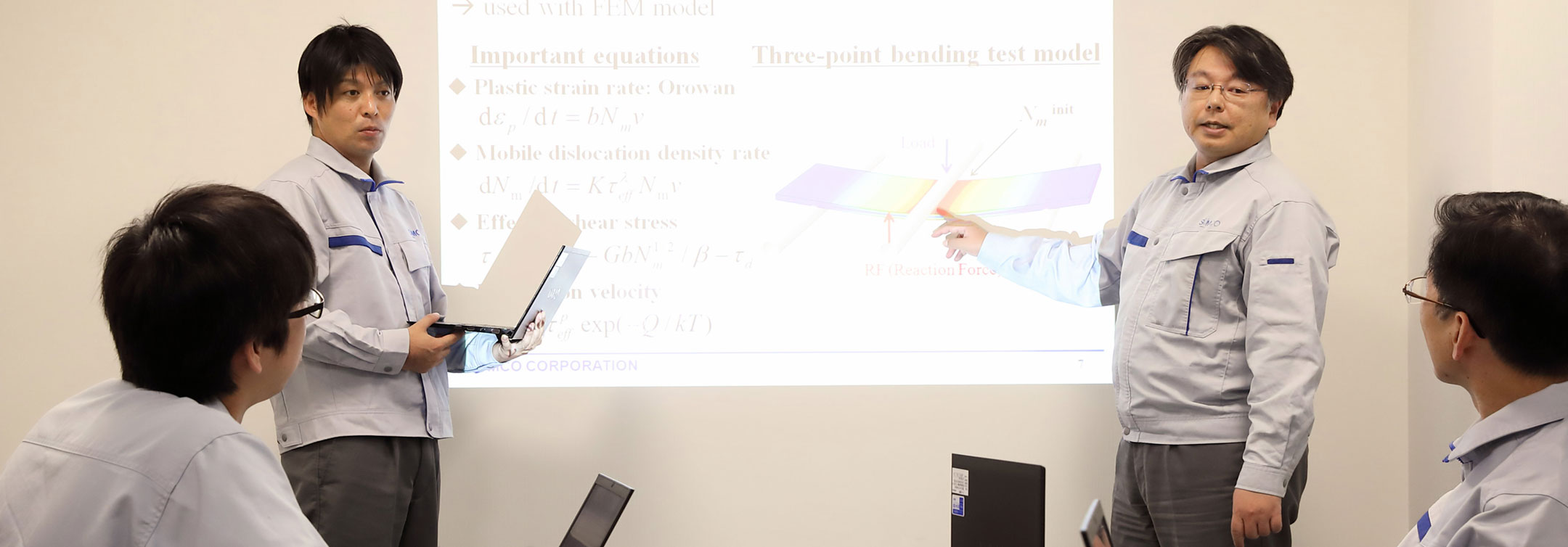
シミュレーションに
必要な基礎データを蓄積。
B.Kが、SUMCOで積み上げてきた知見を活かしながらプログラム開発に励む一方で、もう一つ重要な業務を担ったのがJ.Fです。シミュレーションに必要な基礎データを蓄積していきました。J.Fはこう振り返ります。
「実際に温度や時間、加熱速度を微妙に変えて何度も実験を繰り返しました。品質が異なるウェーハを対象にした試作は300検体に上ります。そこで得た膨大なデータをシミュレーションシステムに取り込むことで、ウェーハ品質の最適化を行い、強度を上げることができます」
SUMCOの強みは部署を超えた連携力にあります。熱処理のウェーハ挙動に影響するデータ収集も例外ではなく、シリコン結晶の品質を決める結晶技術部や、ウェーハの形状を決めるウェーハ技術部の視点などが反映されました。他部署からの声は、B.Kのプログラム開発にも活かされています。
SUMCOの団結力とシミュレーションシステムの開発に関して、T.Oには忘れられない出来事があります。
2010年、シミュレーションシステムの分析をもとに、海外の半導体メーカーにウェーハの仕様変更を提案しました。「本当に問題はないですか?YesかNoかで答えてください」。そう問われたT.Oは戸惑いながらも、“Yes”と言い切りました。部署をまたいだ自分たちの奮闘に自信があったからです。返答は「I trust you」というもの。「“Believe”より信頼性の重さを感じる“Trust”の言葉に胸が熱くなりました」と、T.Oは笑みをこぼしながら振り返ります。
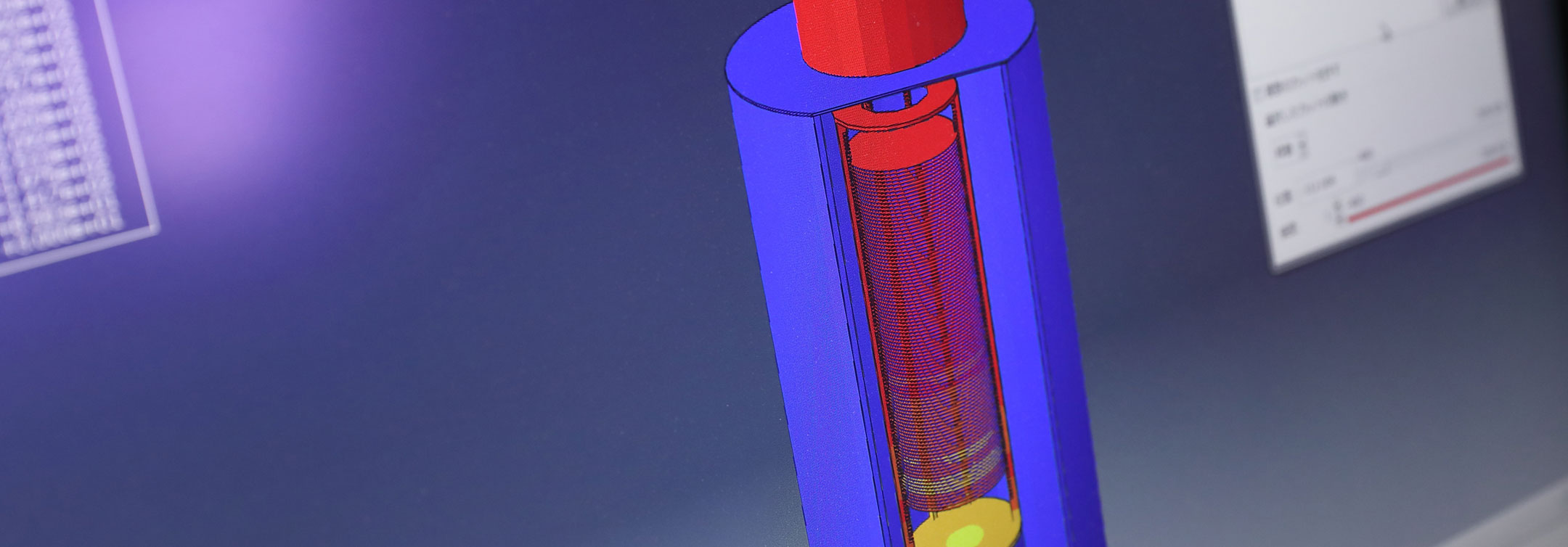
シミュレーション技術を
磨き続けていく。
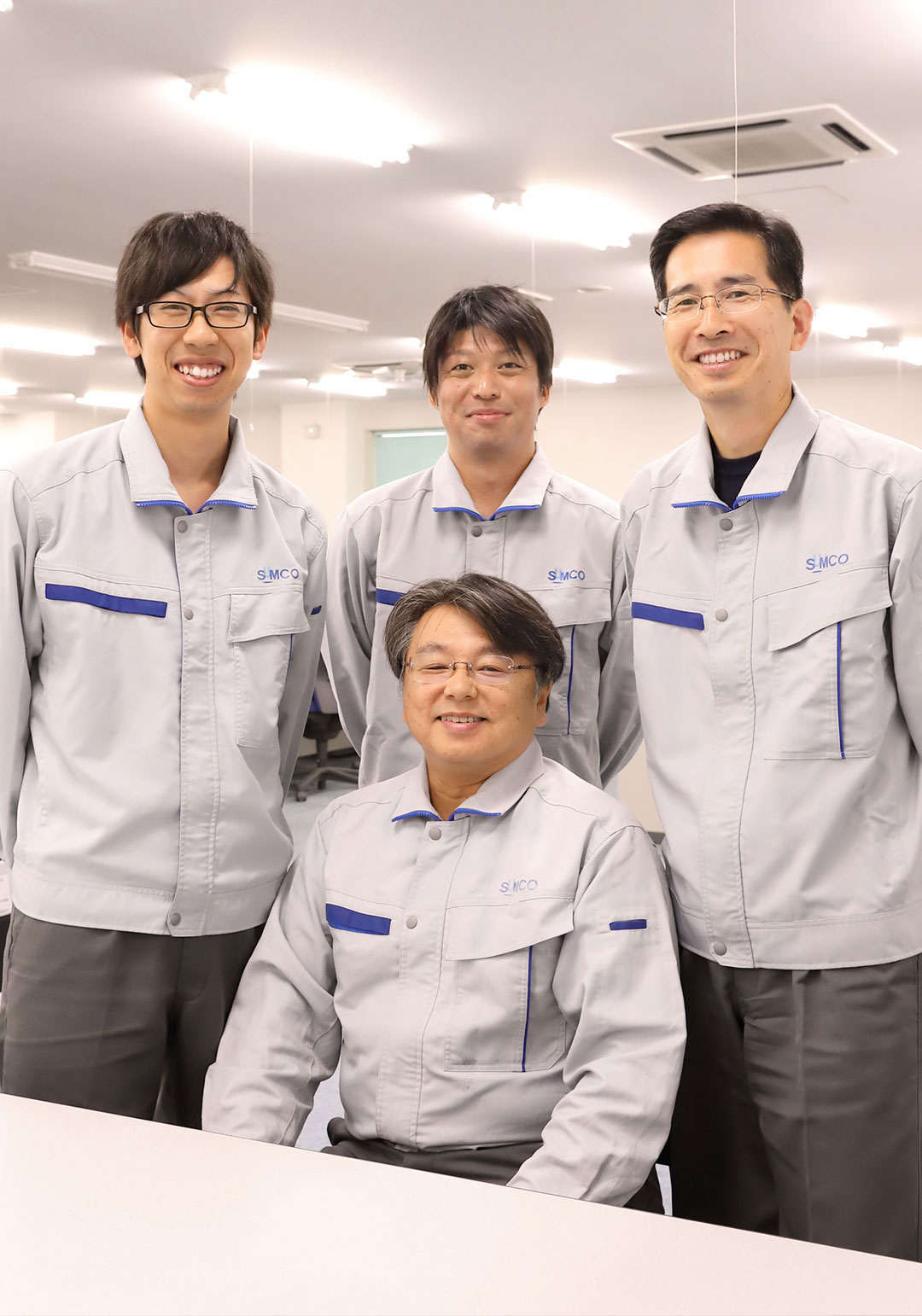
お客様との打ち合わせで得たヒントをもとに熱処理の条件を推察し、そのデータからシリコンウェーハ製造の最適解を導き出す。プロジェクトリーダーのT.Oが顧客から“Trust”という言葉を引き出してからも、理想形にたどり着くまでの挑戦は続きました。最初は「本当にできるのだろうか」という心細さを感じたB.Kが、SUMCOの知見を頼りにプログラム開発に打ち込み続け、J.Fは基礎データを蓄積するために、来る日も来る日も実験と分析を繰り返しました。他部署の協力を得ながら、シミュレーションシステムが一定の成果を上げるようになったのは2015年ごろのことです。
プロジェクトの立ち上げから10年にもおよんだ取り組みは、確実にSUMCOと社員の成長を促しました。「世界的な半導体メーカーの方から、相談をいただく回数が増えました」と手応えを話すのはB.K。「シリコンウェーハの強度に関する専門家」と認識されるようになったJ.Fは業務の傍らで、大学院の博士課程で学んでおり、会社への貢献度をより高めたいと考えています。
2016年入社のK.Tは、システムの精度向上やシミュレーション対象の拡張を担当。実際の実験データとシミュレーションの結果を比較分析する中で、さらなる進化を見据えています。また最新の半導体プロセスの技術動向をシステムに反映させることで、常に先端プロセスに対応しようと試行錯誤を繰り返しています。
「半導体の回路はどんどん微細化しているので、ウェーハに関しても従来より小さな傷やゆがみをシミュレーションできるようになりたいです。今は1,000分の1mmまではわかりますが、今後は10,000分の1mmをめざしたいです」
リーダーを務めるT.Oの向上心も尽きません。T.Oは凛とした顔つきでこう話します。
「半導体の加工は熱処理だけに限りません。レーザーや微粒子を用いた処理もあります。多様化する加工技術に対応するために、今後はシミュレーションができる幅を広げなければ、と考えています」
技術で世界一の会社。SUMCOのビジョンの一つが、これからも前人未到の挑戦を後押ししていきます。