Steady Progress in Digital Transformation (DX)
Under the SUMCO Vision, SUMCO aims to be a leading company in the area of digital transformation (DX). We established the AI Promotion Division in 2018 and have actively pursued initiatives such as building a system to analyze and predict improvements in productivity and quality in real-time by collecting quality and process information for each stage of the production process as Big Data. We are also working to improve equipment productivity and labor productivity, aiming to enhance competitiveness in areas with the most in-demand commodities and strengthen our profit base.
DX Promotion Strategy
At SUMCO, we are working to achieve real-time monitoring and automation of production processes and to establish a production capability and production plans capable of flexibly meeting market demand fluctuations. We are also seeking to expand the areas where AI is employed. By realizing rapid data analysis in the technology fields of our leading-edge products, and speeding up the time from development to mass production, we aim to enhance the agility and competitive advantage of the entire organization through the promotion of DX.
Successes and Extent of Achievement to Date
Development of an AI-based Management System for High-Precision Products
As a specific example of our initiatives, we have developed an automated analysis and evaluation system that utilizes AI-based judgment using real-time monitoring (RTM) data. Traditionally, quality determination required manual inspection by experienced engineers. By developing this system, we have automated this task, significantly contributing to improved yield and quality of high-precision products. Furthermore, we have successfully reduced engineer work-hours by more than 2,500 hours annually.
Operation Efficiency Through DX Tools and Other Solutions
DX tools is the general term used at SUMCO for tools that support operation efficiency, including BI tools,*1 RPA,*2and workflow systems*3.
The results so far are work savings of more than 163,000 hours a year.
By continuing to introduce DX tools of various kinds and making them a regular part of operations, we will seek to improve product quality along with work efficiency.
DX Education
To enhance our corporate value and secure a competitive advantage, it is essential to improve the efficiency of each business process through innovation. For this purpose, each employee is required to improve their skills, view every issue as their own, and proactively work towards solving them. SUMCO positions DX promotion as a crucial means of supporting problem-solving and focuses on DX education to enable all employees to engage in DX initiatives.
1) Division SE system
From each department and division of the plant, non-IT personnel will be accepted as internal exchange students by the AI Promotion Division. After conducting education and training on practical IT and DX tools, essential for manufacturing and business operations, participants return to their respective departments and divisions and play active roles as key figures in continuing to promote DX. This system started in 2021 and has produced approximately 40 graduates.
2) IT roundtable project
The project members consist of employees recommended from various back-office departments, and they regularly conduct study sessions on IT and DX. The project members actively engage in business improvement using IT and DX tools, based on the PDCA cycle from issue identification to enhancement, as a practical learning approach. Information Systems Department provides them with accompanied supports. Additionally, the project members implement the outcomes of business improvement efforts in their respective departments and actively pursue new initiatives within them. This project started in 2023 and is currently continuing with the business improvement activities of the second generation.
(3) DX education for all employees, along with encouragement and incentives for obtaining IT certifications
SUMCO offers DX education aimed at enhancing the DX skills of all employees. We provide education not only to improve basic IT and DX tool skills but also to enhance understanding of the necessity of IT and DX at SUMCO, raise IT and DX literacy, and foster a culture that embraces new challenges. Furthermore, we have enhanced the incentive rewards for passing the Japan Information Technology Engineers Examination, which is a national qualification examination, establishing a system that supports employees' self-improvement and skill acquisition.
Obtaining DX Certification
As a result of these efforts, SUMCO has been selected as a "DX Certified Operator" by the Ministry of Economy, Trade and Industry’s Digital Transformation Certification, recognizing that SUMCO has the vision, strategy, and framework, etc. necessary to transform its business through digitalization.
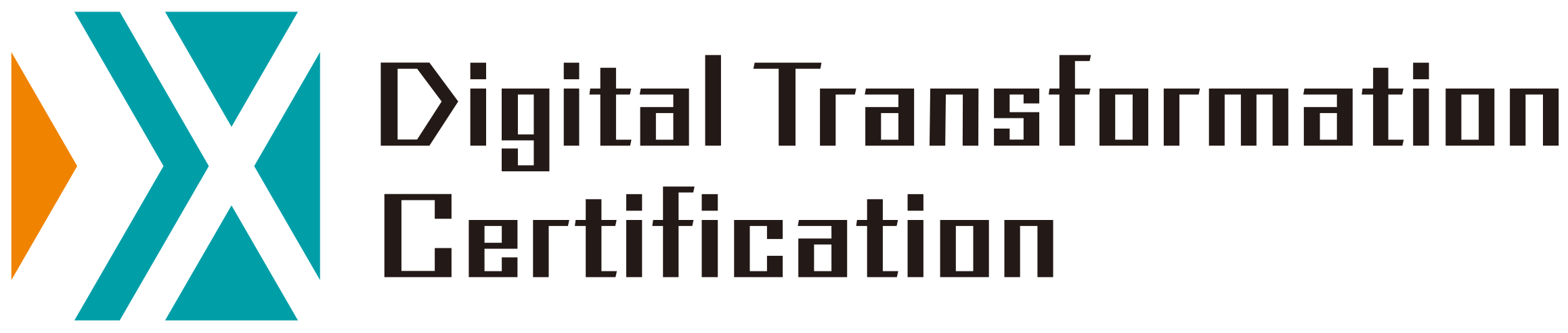
Adapting flexibly to different work styles in the “new normal” era
Even before the pandemic, we had introduced a secure remote work system from the standpoint of BCP (business continuity planning). Taking advantage of this system, we switched to a full teleworking arrangement in the Tokyo region from the beginning of April 2020, ahead of the first state of emergency declaration. (Currently, a combination of office work and teleworking is in use.)
We also utilizes web conference tools for meetings related to management decisions, and management has continued to be carried out seamlessly making use of the electronic approval system already in place.
While adapting to work styles for a new era, we will continue implementing measures aimed at achieving a high level of diversity.
- *1 BI tools(BI = Business Intelligence)
- Tools used to collect and analyze various data in support of on-site and management decision making.
- *2 RPA(RPA = Robotic Process Automation)
- Technology for automating computer-based processes and tasks to replace human labor.
- *3 Workflow system
- A system that computerizes various requests in an organization to make the checking and approvals process more efficient.